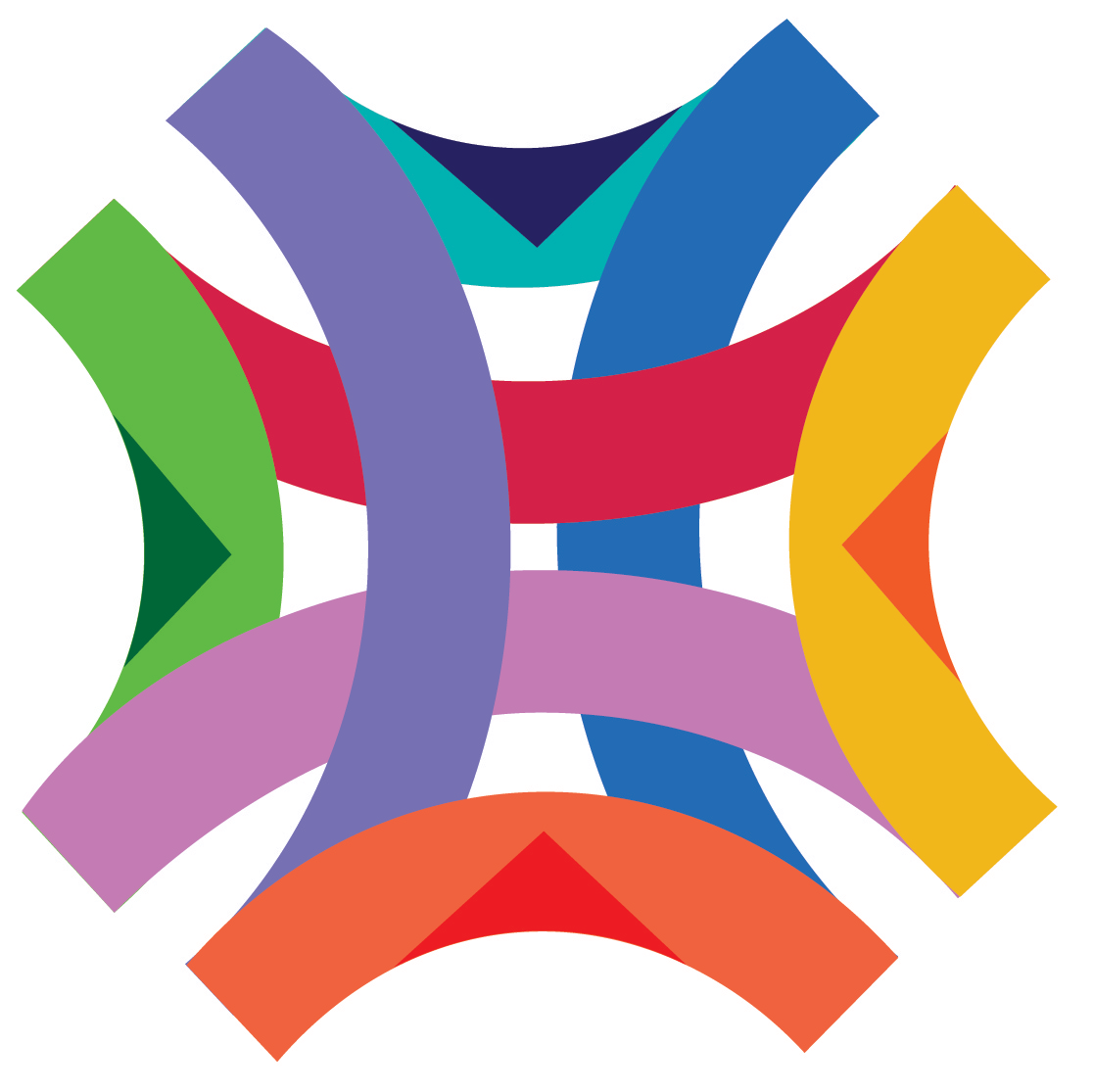
专访安徽大学朱凌云:研发绝非“一蹴而就”,全固态电池尚未达到理想状态
近日,工业和信息化部(以下简称“工信部”)正式发布强制性国家标准《电动汽车用动力蓄电池安全要求》(以下简称“电池新国标”),该标准将于2026年7月1日起正式实施。传统液态电池的安全隐患始终难以根除,其能量密度正逐渐接近理论上限,而在低温环境下其性能也难以满足电动汽车需求。在此背景下,全固态电池凭借其高能量密度和卓越的安全性等优势,成为“下一代电池技术”的重要发展方向。然而,全固态电池领域的研究长期以来一直受到固态电解质材料电化学性能、固固界面稳定性以及其产业化工艺等难题的制约。“全固态电池的研发绝非一蹴而就,我始终认为这是一项复杂且具有挑战性的工作。”朱凌云介绍道,目前,其团队主要聚焦于硫化物电解质的研究,团队规模约为20人。硫化物电解质因其卓越的离子传导率以及其优异的界面可调控性能,被广泛认为是极具产业化前景的全固态电池技术路线。时代周报:全固态电池主要拟解决什么问题?您团队在固态电池领域的研究方向是什么?在硫化物固态电解质的研究领域,提升其锂离子传导率的同时,抑制硫化氢的生成是一个至关重要的课题。由于硫化氢具有危险性,因此提升材料在空气中的稳定性,尤其是对微量水分的耐受性,已成为我们实验室当前研究的重点。我们研发出了一种新型配方,可将硫化氢的生成量降低至普通未改性材料的十分之一以下。时代周报:近期工信部拟将“电池不起火”纳入强制标准,引发行业热议。全固态电池如何实现安全性的突破?目前其在热稳定性方面,以及充放电过程中是否仍存在安全隐患?虽然我们可以研发使用不可燃的电解质材料,但在充放电过程中,电池内部仍有形成新的金属锂枝晶风险。理论上,由于锂的还原性极强,新生态的锂会导致部分电解质变质,一旦电池破损泄漏接触空气,电池还会起火。因此,如何抑制金属锂枝晶的产生,将是液态电池和近未来的全固态电池都需要面对的共同挑战。时代周报:当前国内外全固态电池的发展现状如何?日韩在全固态电池技术上与我国的差距如何?哪个国家目前在技术上处于领先地位?在国内,从设备和工业能力来看,并不逊色于日本的电池公司。在研发人员方面,像宁德时代、比亚迪和国轩高科等电池企业,都已组建了几百人规模的团队研发生产全固态电池,进展也比较顺利。同时国内新兴企业不断涌现,还有院士团队牵头投资的企业,发展势头强劲,众多的企业即将下线全固态电池产品。时代周报:对于固态电解质和电极界面间的相容性问题,目前存在哪些难点?有哪些创新的解决思路?全固态电池技术从实验室迈向产业化,需要攻克哪些关键技术?产业化过程中哪些环节最为重要?在实验室中,通常借助 300 兆帕的高压实现电池界面的完美结合。然而,工业化批量生产时,压力需要控制在 5 兆帕以下,而且还需保证这些固固界面不会随电池充放电时材料的膨胀和收缩引起电池边缘开裂等新状况的产生。时代周报:全固态电池对正极材料和负极材料的要求有哪些改变?硫化物路线的稳定性和成本问题是否有解决方案?而从追求更高能量密度的角度出发,磷酸铁锂受其理论比容量的限制,将不会是固态电池正极材料的理想选择。未来,高容量的正极材料,如硫化合物或硫黄等,可能是固态电池正极材料的发展方向。产业化挑战与应用前景展望朱凌云:全固态电池的制备工艺研究目前面临一个关键问题:采用与传统电池相近涂布工艺,很难找到一种适合硫化物电解质特性的溶剂,使其在与硫化物电解质接触时不会降低其锂离子传导性。因此,从面向未来产业的观点来看,固态电池的生产最好采用干法工艺,如干法正极、干法负极和干法电解质膜。在实验室中,全固态电池研究已接近瓶颈。实验室设备资源有限,若要扩大研究规模,如试验制备少量软包电池,低露点的干房和大压力的复合设备都需要与企业联合研究。然而,众多的小型企业也缺乏相应设备,且不太可能投入大量资金购置专用设备。此外,下一步全固态电池的极片内串复合叠加结构的研究,电池极片之间完美的界面结合是制备工艺中的巨大挑战,现有大学的实验室设备难以满足进一步研发的需求。朱凌云:这种观点具有一定的合理性。据我估计,今年或许多家企业的全固态电池的容量可能达到20安时以上,也将能推出和下线真正意义上的全固态电池。预计到2027年,固态电池将能实现小批量装车。尽管这并不意味着大规模应用,但至少可以证明全固态电池在2030年之前有望在市场上占据一席之地。
从实验室研究的角度来看,若要实现大规模应用,全固态电池最理想的优先应用场景应该是3C消费电子领域。小型全固态电池的10分钟快充特性,非常适合手机用户对电池性能的使用要求。
还没有评论,来说两句吧...